Types of Refractories: Refractories are used in all kind of industries with the furnace to reduce the heat loss. The used refractory properties required for each kiln/furnace varies based on the application. So different refractories are used to provide unique properties. In this article, we are going to see all types of refractories available in the industry.
Manufacturing Process:
Generally most of refractory brick have this similar type of manufacturing process except one or two.
Raw Material Processing:
The raw material for the refractory brick is processed to remove the impurities.
Mixing:
Then the processed raw materials is mixed is either done in Muller or counter flow mixer for 10-20 minutes.
Shaping:
Shaping is done by pressing or casting.
The method of shaping depends on
- Water present
- Dimension and size
- Productivity
Drying:
Drying is done to remove the physically combined water molecules. Drying is done in 2 steps.
- Natural Drying
- Oven Drying.
Natural Drying is done for 48hrs at room temperature.
Oven Drying is done for 150-250â—¦ C for 20 to 30 hrs. Drying is done slowly to avoid formation of cracks.
Firing:
Firing is done to remove chemically combined water and to increase the strength of the refractory brick.
Finishing:
Finishing process consist of cutting, milling, drilling. It is dine for removing or smoothening any surface.
Inspection:
The fired refractory bricks are visually inspected for presence of cracks or any defects
Testing:
The inspected refractory bricks are then tested to check if it is having some specific property to use that brick in some fields.
Types of Refractories
Silica Refractory:
Silica refractory products consist of 93% silica. They are the most widely used high-temperature refractory bricks. They are acidic refractories, they resist acidic slag attack but attacked by basic slags. Depending on the final we can two final products. If the final temperature is 1430â—¦ C the product is tridymite. If the final temperature is 1480â—¦ C then the final product is cristobalite.
Â
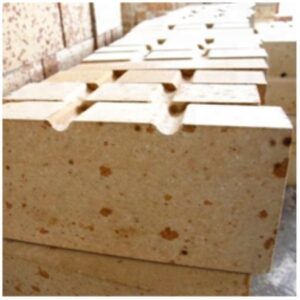
Raw Materials:
- Quartzite
- Lime
Quartzite:
Quartzite is a secondary form of quartz. They are formed from a metamorphic rock. They are a dense agglomerate of quartz boded by finely divided silica.
Lime:
Adding lime will increase the green strength of silica refractory. They also act as mineralizer (Enhance the phase transformation of silica).
Properties:
Chemical Composition | |
SiO2 Content | 90-97% |
Al2O3 Content | 0-0.4% |
MgO Content | 0.15-0.20% |
CaO Content | 0.30-0.40% |
CrO Content | 0-0.5% |
SiC Content | 0-0.02% |
Physical Properties | |
Colour | White |
True Density | 2.30-2.40 g/cc |
Bulk Density | 1.8 g/cc |
Â
Thermal Properties | |
Refractoriness | 1700â—¦C – 2000â—¦ C |
Â
Applications:
They are used in
- Upper checker work in hot blast stove
- Coke Ovens
- Glass furnace crown
Price:
Price of one silica refractory brick is between $0.10-0.70
High Alumina Refractory:
High alumina refractory contains more than 45% Al2O3. They are mostly used in high-temperature applications. They withstand high temperature, they have good corrosion and wear resistance, and low iron content. They are used in mining, metallurgical industries.
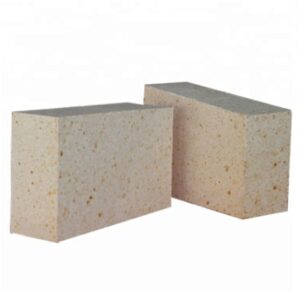
Â
Raw Materials:
- Natural
- Synthetic
Natural Raw Materials:
- Siliminate
- Hydrated Alumina
Synthetic Raw Material:
- Calcined Alumina
- Fused Alumina
Types of High Alumina Refractory:
- Siliminate based High Alumina Refractory
- Mullite based High Alumina Refractory
- Bauxite based High Alumina Refractory
- Corundum based High Alumina Refractory
Siliminate based High Alumina Refractory:
Manufacturing process:
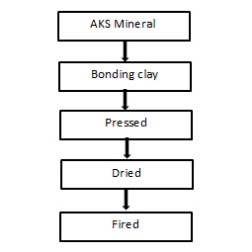
If Siliminate is used, the resultant product will have,
- High Toughness
- High Strength
- Corrosion Resistance
Mullite based High Alumina Refractory:
 For Refractory we use
- Sintered Mullite
- Fused Mullite
 Manufacturing Process:
If Mullite is more, then the resultant product will have
- Low thermal conductivity
- Low slag resistance
Bauxite based High Alumina Refractory:
Manufacturing Process:
If bauxite is used, the resultant product will have
- Less than 5% SiO2
- Less than 3% Fe2O3 and TiO2
Corundum based High Alumina Refractory:
Manufacturing Process:
If corundum is used, the resultant product will have
- High strength
- High corrosion resistance
- High thermal conductivity
Properties:
Chemical Composition | |
SiO2 | – |
Al2O3 | 40-90% |
MgO | 0.5-1.5% |
CaO | 0.30-0.40% |
CrO | 0-0.5% |
SiC | 1-1.5% |
Fe2O3 | 2-2.3% |
Â
Physical Properties | |
Colour | White |
Porosity | 20-25% |
Crushing Strength | 30-70Mpa |
Â
Thermal Properties | |
Refractoriness | 1550-1800â—¦ C |
Application:
- Electric arc furnace roof
- In petrochemical industry
- Blast furnace stove
Price:
Price of high alumina refractory brick is $100-500 per ton.
Magnesite Refractory:
Magnesite is a group of carbonate mineral. Its formula is MgCO3 with MgO 45-50% and CO2 50-55%. They are unreactive to carbon dioxide. They have a high melting temperature and they are on-toxic in nature. They resist alkali slag attacks.
Raw Materials:
Mostly Magnesite is derived by calcination of MgCO3 and Mg(OH)2
The other important sources are
- Dead burnt Magnesia
- Fused Magnesia
Properties:
Chemical Composition: | |
SiO2 | 0% |
Al2O3 | 0-0.2% |
MgO | 90-97% |
CaO | 0-3% |
CrO | 0-0.3% |
SiC | 0-0.2% |
Â
Physical Properties: | |
Apparent Porosity | 15-20% |
Bulk Density | 2.8-3.2g/cc |
Cold crushing strength | 40-90 Mpa |
Â
Â
Thermal Properties: | |
Refractoriness | 1750-2000â—¦ C |
Â
Applications:
Magnesite bricks are mainly used as
- Thermocouple tubes
- Crucibles
- Heating element
- Plasma display screens
Price:
Price of the magnesite refractory brick is $ 900-1300 per ton.
Forsterite Refractory:
Forsterite is one of the magnesium silicate types of refractory. Its formula is 2MgO.SiO2with 60-70%MgO and 15-20% SiO2which has stable existence above 1600â—¦ C. They have high refractoriness, high temperature strength, resistance to basic slag erosion resistance, excellent thermal stability, acidic slag also has some adaptability
Raw Materials:
- MgO
- SiO2
- Kaolin
Properties:
Chemical Composition | |
SiO2 | 0-20% |
Al2O3 | 0-25% |
MgO | >60% |
CaO | 0-0.4% |
CrO | 10-15% |
SiC | 1-1.5% |
Â
Physical Properties | |
Colour | Red firebrick |
Apparent Porosity | 15-20% |
Bulk Density | 2.8-3.3g/cc |
Cold Crushing Strength | 38-43Mpa |
Â
Thermal Properties: | |
Refractoriness | 1550-1800â—¦ C |
Â
Applications:
- Used in electronic substrates
- Used in solid oxide fuel cells
- An electrical insulator at a high temperature
Price:
The price of one refractory brick is $400-1300 per ton.
Dolomite Refractory:
Dolomite bricks are made up of MgO 25-45%, CaO 35-65%, and other materials.
They have high refractoriness, Thermal stability at high temperature and slag resistance. They are more porous, more shrinkage softness and less strong. They can be used up to 2300oC without load and up to 1650oC with the load.
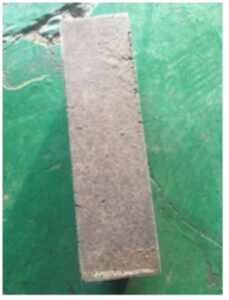
 Raw material:
- Calcined dolomite
- Binders
- Water
Properties:
Chemical Composition: | |
SIO2 | 3-4% |
Al2O3 | 0% |
MgO | 60-70% |
CaO | 30-35% |
CrO | 0% |
SiC | 0% |
Physical Properties: | |
Colour | Grey |
Apparent Porosity | 2-4% |
Cold Crushing Strength | 60-65Mpa |
Thermal Properties: | |
Refractoriness | 1750-2000â—¦ C |
Â
 Applications:
- Mostly they are used in iron and steel industries
- They have good corrosion resistance
Price:
The price of dolomite brick is $ 1800-1900 per ton.
Magnesia Chrome-based Refractory:
Magnesia chrome refractories are basic refractories generally composed of magnesia and chrome. They have good thermal spalling resistance. The low basic neutral nature gives good slag resistance when servicing low acid feed furnaces. Brick is a practical lining material for refining furnaces, electric furnaces, glass melting furnaces and cement rotary kilns.
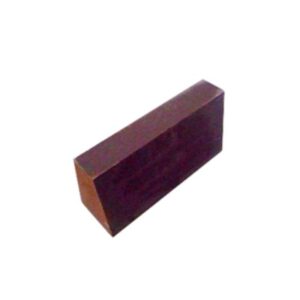
Raw Materials:
- Sintered Magnesia
- Chrome
- SiO2
- CaO
Properties:Â
Chemical Composition: | |
SiO2 | 1-3% |
Al2O3 | 1-2% |
MgO | 60-95% |
CaO | 1-3% |
CrO | 0-0.3% |
SiC | 0-0.2% |
Â
Physical Properties: | |
Colour | Brown |
Apparent Porosity | 16-18% |
Bulk Density | 3-3.3g/cc |
Cold Crushing Strength | 30-50Mpa |
Thermal Properties: | |
Refractoriness | 1550-1800â—¦ C |
Applications:
They are used in
- Glass furnace
- Electric arc furnace
- Metallurgical applications
Price:
The price of magnesia chrome refractory is $ 400-1300 per ton.
Magnesia Carbon based Refractory:
 Magnesia-carbon refractory is high melting basic refractory. They have high corrosion and erosion resistance, good thermal shock resistance and high volume stability and used for normal carbon and high carbon steel production.
Raw Materials:
- Sintered Magnesia
- Carbon
- Synthetic tar binder
Properties:Â
Chemical Composition: | |
SiO2 | 0% |
Al2O3 | 0-0.2% |
MgO | 80-85% |
CaO | 0% |
CrO | 0-0.02% |
SiC | 0-0.02% |
Â
Physical Properties: | |
Colour | Black |
Bulk Density | 2.6-3.2g/cc |
Cold Crushing Strength | 30-70Mpa |
Thermal Properties: | |
Refractoriness | 1750-2000â—¦ C |
Applications:
- Water cooled electric furnace
- Basic oxygen converter
- Ladle slag lines
- Degassers
Price:
The price of magnesia based carbon refractory brick is $ 900-1300 per ton.
Zirconia Refractory:
Zirconia bricks are the bricks which have more than more than 65% of ZrO2. They have good thermal shock and good corrosion resistance. Primarily used for the key parts of the furnace of glass furnace, glass fiber furnace,garbage incinerator furnace, electrothermal furnace,etc.
 Raw Materials:
- Zircon
- Cubic zirconia
- Other binders.
zirconia type of refractories
 Properties:
Chemical Composition: | |
SiO2 | 0-20% |
Al2O3 | 0-60% |
MgO | 0.5-2% |
CaO | 0-0.4% |
CrO | 0-0.3% |
SiC | 1-1.5% |
ZrO2 | 0-65% |
Â
Physical Properties: | |
Apparent Porosity | 15-20% |
Bulk Density | 2.7-6.5% |
Cold Crushing Strength | 100Mpa |
Thermal Properties | |
Refractoriness | >2000â—¦ C |
Â
Applications:
- Used in glass furnace
- Used in ladle lining for metallurgical industry.
- Used in steel industries
 Price:
The price of zircon refractory is $ 25000-65000 per ton.
Fused cast AZS Refractory:
Fused cast is the process in which the raw materials are heated up to 2000â—¦ C, cooled and casted. These refractory have 0% porosity. They have Strong glass corrosion resistance and high thermal shock stability. Good wear-resistance, drags-resistance and alkali corrosion resistance.
Â
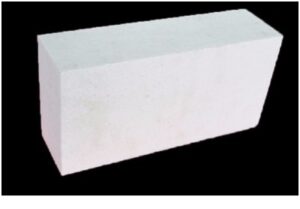
Raw Materials:
- Silica Sand
- Zirconia bubbles
- Bubble Alumina
- Fume Silica
Properties:
Chemical Composition: | |
SiO2 | 14-16% |
Al2O3 | 45-50% |
MgO | 0% |
CaO | 0-0.5% |
CrO | 0% |
SiC | 0-1.5% |
ZrO2 | 30-35% |
Â
Physical Properties: | |
Colour | White |
Bulk Density | 3.5-3.75g/cc |
Cold Crushing Strength | 340-360Mpa |
Â
Thermal Properties: | |
Refractoriness | 1750-2000â—¦ C |
Application:
- They are generally used in a glass furnace.
Price:
The price of the refractory brick is $ 2000-3200 per ton.
Monolithic Refractory:
Monolithic refractories are the unshaped refractories. They do not shaping ad firing, so energy and time will be saved.
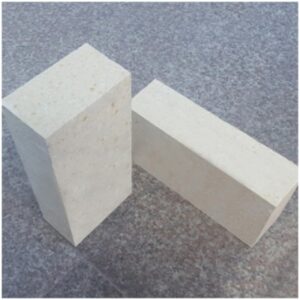
Types of monolithic refractories:
- Castables Refractory
- Plastic Refractory
- Ramming mixes
- Gunning mixes
- Refractory Mortars
 Properties:
Aluminum based monolithic bricks have
Chemical Composition: | |
SiO2 | 0-5% |
Al2O3 | 45-90% |
MgO | 0-0.05% |
CaO | 0-0.05% |
CrO | 0-0.005% |
SiC | 0-0.02% |
Physical Properties: | |
Colour | Yellow |
Porosity | 15-25% |
Cold Crushing Strength | 40-90Mpa |
Â
Thermal Properties: | |
Refractoriness | 1750-2000â—¦ C |
Applications:
- They can be easily installed
- They are used in anchoring systems
- They are used in petroleum industries
 Price:
The price of one aluminum based monolithic refractory brick is $ 20-90 per brick.
Insulating Refractory:
 Insulating bricks are lightweight bricks with low thermal conductivity.
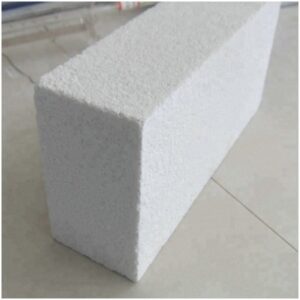
There are different types of refractory bricks
- low strength
- high strength
- low ferrous
- high ferrous
Raw Materials:
- Calcined fireclay
- Aluminium sulphates and phosphates
 Properties:
Low iron insulating bricks have
Chemical Composition: | |
SiO2 | 45-70% |
Al2O3 | 40-45% |
MgO | 0.5-1.5% |
CaO | 0-0.02% |
CrO | 0-0.3% |
SiC | 0-1.5% |
Fe | 0-2% |
Physical Properties: | |
Colour | White |
Porosity | 0-26% |
Bulk Density | 2.10-2.25g/cc |
Â
Thermal Properties: | |
Refractoriness | 1550-1800â—¦ C |
Application:
- Used For Insulation purpose
Price:
The price of the low iron insulating brick is $ 80-720 per ton.