In this article, we are going to see about step by step manufacturing process of float glass. Float glass is a widely used glass which is made of sodium silicate and calcium silicate. This glass is inexpensive and also called as window glass/ flat glass/ plate glass.
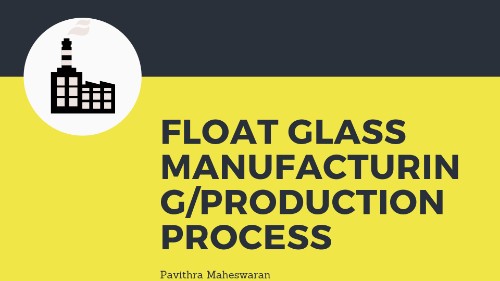
Now we will discuss the entire production of float glass manufacturing in a stepwise manner.
BATCHING OF RAW MATERIALS
- The raw materials used in float glass manufacturing are silica sand, calcium oxide and magnesium, soda ash, and feldspar.
- As we know that sand (73%) is the body former in the glass. It is the primary raw material of glass; calcium oxide (9%) and magnesium oxide (4%) to reduce solubility; soda ash (13%) to lowering the melting point; feldspar (2%) to increase the hardness.
- The above-said ingredients are fine-grained, weighed and mixed to make batches to which the cullet is also added. Here, the purpose of cullet is to reduce the consumption of natural glass. The next step is melting.
MELTING
- In this melting process, the batched raw materials are then passed to a melting furnace for 50hours at a temperature of about 1500oC where they become molten.
- The molten glass which is free from inclusions and bubbles.
- If certain metal oxides are mixed, they impart colors to the glass by giving a tint body. The cullet in melting process acts as a flux to reduce the melting point of the batching raw materials.
REFINING
- We know that the refining process is a purification process which is done at the furnace to remove unwanted elements or impurities present in the molten glass.
- If they were not removed, a grain of sand is refused to melt.
FORMING
- The molten glass is fed into the tin bath (float bath) under the controlled atmosphere of N2/H2 gas to prevent oxidation of tin and the glass flows onto the surface of tin at a temperature of about 1000o
- Then it forms a solid ribbon at 600oC with a perfectly smooth glossy surface with the even thickness which is highly viscous.
- The density of glass should be lower than that of tin. Here, some specifications are: length = 50m, width = 3-4 m, depth = 6cm
- The tin bath has three different zones separately: Heater zone, Fire polish zone, and Cooling zone.
Why tin bath is provided in float glass manufacturing?
Tin is suitable for this type of glass manufacturing, because of its higher specific gravity. It is oxidized in a natural atmosphere to form tin oxide (TiO2). Hence, to prevent oxidation, tin bath is provided with pressure and; hydrogen and oxygen as a protective atmosphere.
ANNEALING
- The formed glass is leaving from the tin bath at a temperature of 600oC
- On cooling the glass, some stresses are developed in the solid ribbon. After that, it is cooled down sufficiently to passed through an annealing chamber (lehr), where the internal stress is removed to improve the glass yield and also ensures the flatness of a glass. If the surfaces are fire finished, they need no grinding and polishing.
- In annealing lehr, cooling can be controlled in 4 to 8 separate zones.
- The glass is passed between rollers into different sections of lehr.
- The first section of lehr which is Ao section maintains a uniform temperature.
- The second section of lehr which is B section, the glass temperature is cooler. This section use both heating and cooling in a controlled process. Permanent stresses within the glass formation can occur at a lower temperature, below its strain point.
- For the manufacturing of float glass, the range of annealing temperature range is from 452oC – 482o This point is also called as stress relief point or annealing point of the glass.
WASHING AND DRYING
- Care should be taken to obtain residue free elimination of sulphide. Now it is suitable for coated glass, white glass, and float glass.
- Washing process can be done without the addition of additives.
- After washing, it undergoes a drying process to remove the undesirable moisture content present in the annealed glass.
DEFECT ANALYSIS
- Quality can be controlled by reducing the defects which are present in the float glass.
- Bubbles, knot, cord, cracks, and seeds are some of the defects which prone to spoiling the end product.
- The other defects like insects, dust are also eliminated.
- To ensure high quality of glass, the inspection must take place at every stage.
- The float glass is checked for any defect present in the glass.
- Both online inspections by computer and manual inspection are also available to enhance the quality of glass and then it is ideal for customer line satisfaction.
- Defected float glass is sent to the recycling process and used as a cullet in batching process.
CUTTING
- The cutting process is done by using a diamond cutter with stressed edges which are dictated by the computer.
- The purpose of using a computer in the cutting process is to meet the customer requirements into patterns of cuts designed to minimal of wastage.
- It is sold by the square meter.
- Individual sheets are separated and packed for further applications.
PACKING
- Based on customer requirements, glasses are packed.
- It is packed with suitable packaging in wooden box to avoid damage during transportation.
CONCLUSION
In this article, we have seen the step by step production of the float glass manufacturing/ production process. The glass manufacturing principle is overall same in different types of glass except one or two.